Are flat sheet "Y"s stronger
Are flat sheet "Y"s stronger
I tried bumping the flat sheet Y thread, seems to be little interest.. I am seriously considering the flat sheet Y. I'd like to learn more, strength changes of angle, sheet thickness "varied" etc. Best type of joins, surface area of welds to downtube etc..
Bearoso has mentioned it a few times, i'd like to learn more. I particularly liked the double bend cradel attached to the down tube directly with massive surface area of welds but i believe the radiators would require extensive modification due to their location. So i believe flat sheet would be next best option..
Bare in mind i will be doing a 125 conversion and will require a change of angle due to sharp down tube. Besides that and my bike aside i'd like to know more regardless of bike. I'm sure their are some great minds on here that could go into further detail..
Bearoso has mentioned it a few times, i'd like to learn more. I particularly liked the double bend cradel attached to the down tube directly with massive surface area of welds but i believe the radiators would require extensive modification due to their location. So i believe flat sheet would be next best option..
Bare in mind i will be doing a 125 conversion and will require a change of angle due to sharp down tube. Besides that and my bike aside i'd like to know more regardless of bike. I'm sure their are some great minds on here that could go into further detail..
13 isnt unlucky i just keep falling off
- Roostius_Maximus
- Site Admin
- Posts: 4641
- Joined: November 16th, 2007, 3:24 pm
- Last active:
- Location: Mt Nebo, Manitoba, Canada
- Contact:
bro and i did one on a 2003 125 chassis, looks good, havent finished the bike tho 

http://www.youtube.com/user/500bigbore
My CR500 Tech Reference... http://sdrv.ms/1a0CIiz
MRE Components... http://sdrv.ms/1bs2zhd

My CR500 Tech Reference... http://sdrv.ms/1a0CIiz
MRE Components... http://sdrv.ms/1bs2zhd

- Roostius_Maximus
- Site Admin
- Posts: 4641
- Joined: November 16th, 2007, 3:24 pm
- Last active:
- Location: Mt Nebo, Manitoba, Canada
- Contact:
i should have used you're drawing. It turned out good tho.
http://www.youtube.com/user/500bigbore
My CR500 Tech Reference... http://sdrv.ms/1a0CIiz
MRE Components... http://sdrv.ms/1bs2zhd

My CR500 Tech Reference... http://sdrv.ms/1a0CIiz
MRE Components... http://sdrv.ms/1bs2zhd

- gregrobo
- Posts: 1064
- Joined: April 18th, 2009, 8:47 am
- Last active:
- Location: kalgoorlie, western australia
i sold the bike with the billet y i built a bike from a 02 crf 450 frame for my cousin we used the stock y and it broke pretty bad
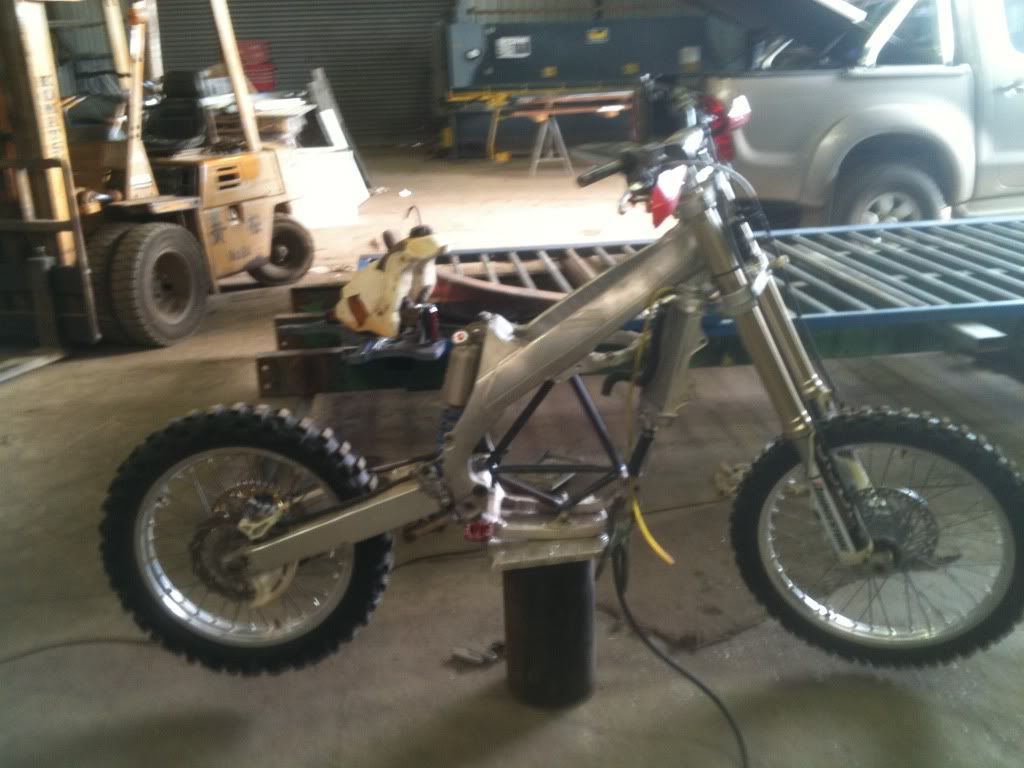
shitty iphone photos
so now i have removed the y and fabricated a sheet y from 4mm ali and have a 2010 rmz 450 conversion in the works
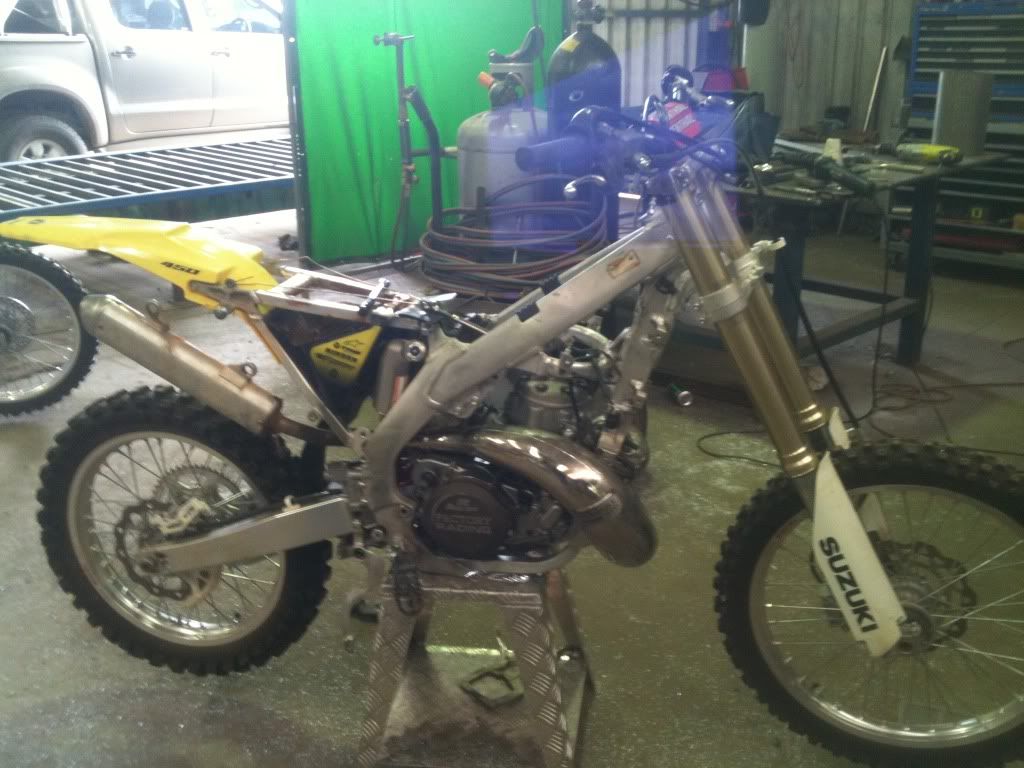
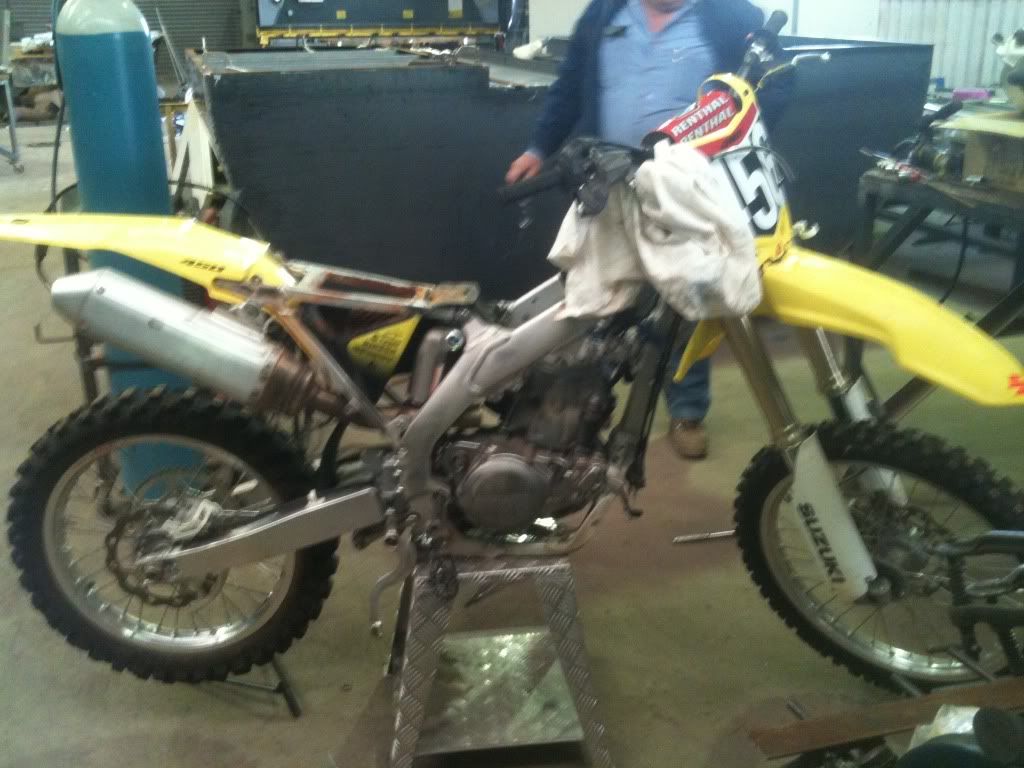
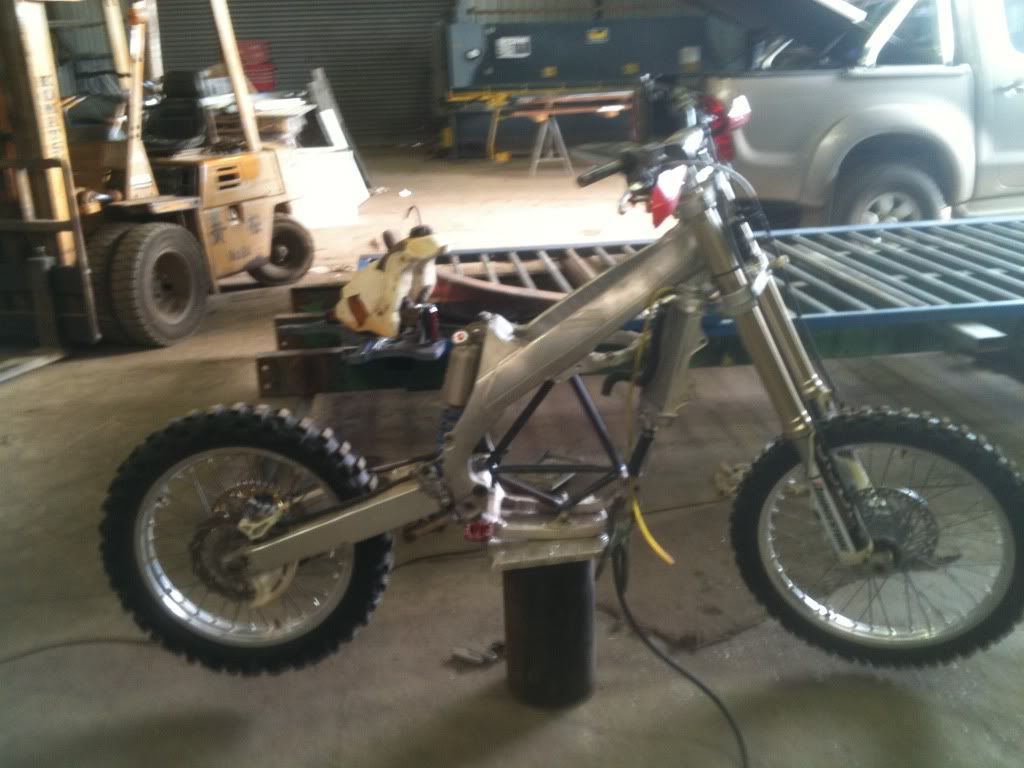
shitty iphone photos
so now i have removed the y and fabricated a sheet y from 4mm ali and have a 2010 rmz 450 conversion in the works
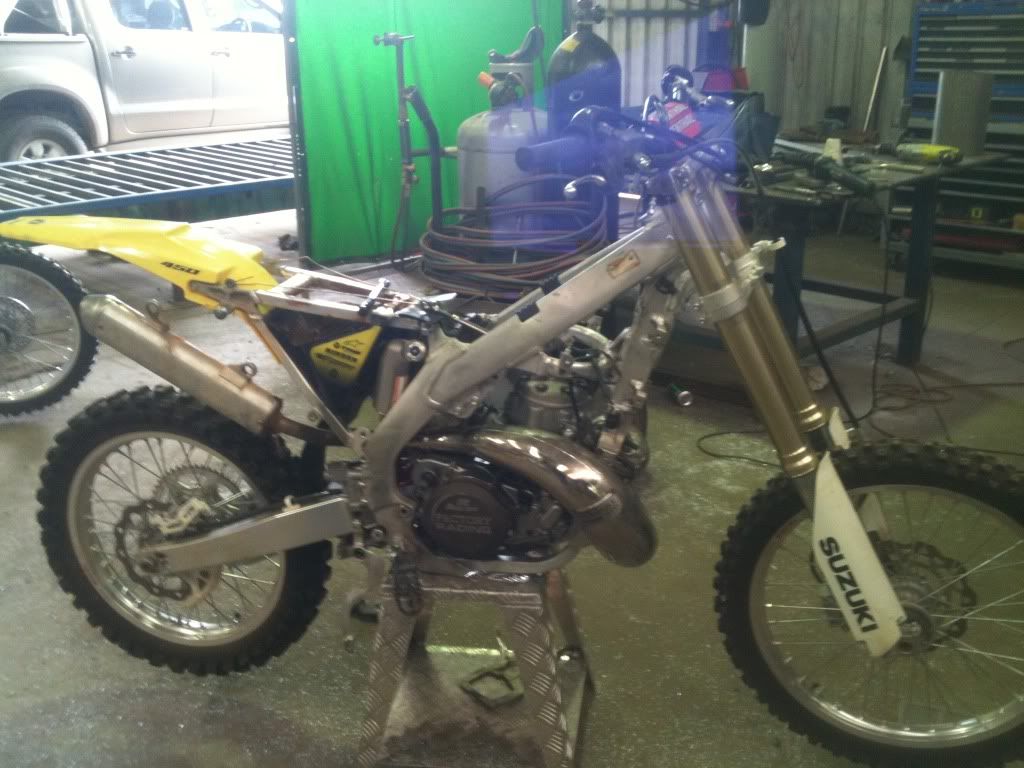
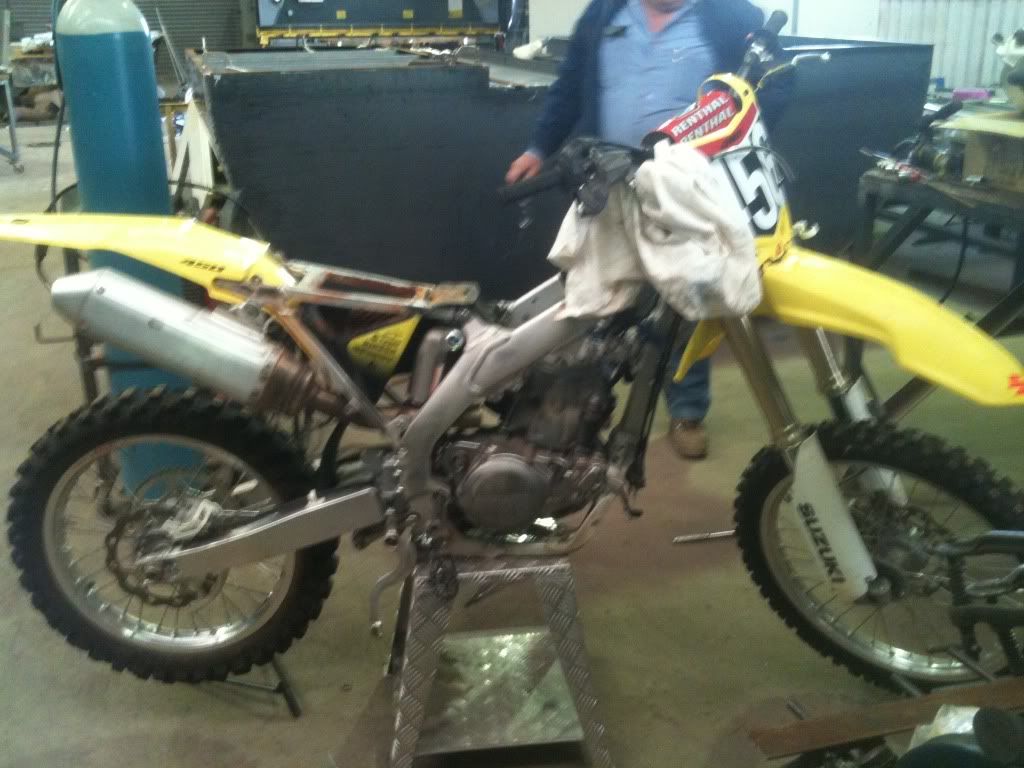
only posties ride 4 stroke hondas
goldfields sheet metal fabrication
98 yzfr1
05 crf 500 race tech goldies
2010 rmz 500af
01 banshee
goldfields sheet metal fabrication
98 yzfr1
05 crf 500 race tech goldies
2010 rmz 500af
01 banshee
Whats these drawings you speak of ?gregrobo wrote:hey roost did you use the drawing i sent you or did you do you own
PS, not sure i like you anymore. I've always secretly lusted for an RMZ. Now i'll probably wanna sell my 125 and get one.

13 isnt unlucky i just keep falling off
Done well, they certainly should be. And they are very good / versatile for 'different' builds - as in, making 'shapes' that might be required, for different frames, like 125s with their more angled back original down tube.
My much preferred option. I think I gave you some direction / suggestions with regards to this on another thread.
My much preferred option. I think I gave you some direction / suggestions with regards to this on another thread.
i've got bits and peices of what you have said, various thickness sheet etc. Care to elaborate? As you can understand the downtube angle change is the major priority.bearorso wrote:Done well, they certainly should be. And they are very good / versatile for 'different' builds - as in, making 'shapes' that might be required, for different frames, like 125s with their more angled back original down tube.
My much preferred option. I think I gave you some direction / suggestions with regards to this on another thread.
I was thinking of the flat Y going over the existing bottom rail, Try and mimick the welds like an OEM Y instead of going with butt welds like most flat sheets i have seen. Would that be prefered? Also regarding sheet thickness, giving the angle etc i assume i would want a thicker section on the front? i am only guessing as the OEM Y has more weld surface area at the front, got me thinking that would be where it sees the most front/back stresses example (suspension and flexing the frame at that point)
Sorry for asking so many questions, i just figure it's best to ask and do it properly... There's an OLD saying "your a long time dead" i dont wish to end up that way if something goes wrong due to the fact it was not built properly.
I hope you understand. Besides if i never ask i'll never learn

13 isnt unlucky i just keep falling off
Have a Squizz at Gregrobo's plate Y build.
I'd take the overlap on the downtube higher ( no problem whatsoever with what he's done, I just tend to go for big engagement - or , idiot overkill as my mates call it), with a 'spear' shape, or a 'U' / 'V' shape at the top. Spear shape - full weld. Longer weld area, without a weld going across the front of the downtube. I've mentioned the risk of welds across a tube in other posts, but, sometimes they are unavoidable. And of no concern.
'U' or 'V' shape, can weld down inside the 'V', same with the 'U', although you could leave the 'inner U' unwelded. I think the downtube gets thinner as you go higher, so if you went high with overlap, you could just go for a very long engagement of the plate, with weld all the way, just up the side / edges. Just a bit of sealant at the unwelded section, would keep crud out, if you chose to go that way.
I'd put a rosette weld on, the base of which I'd have probably an inch away from the edge in the OEM downtube on there. If you had very long engagement, with no cross weld, perhaps another, small rosette weld towards the top, would be the go.
As you can see, with Gregrobo's and others, you can get a very large section Y made, with a lovely shape tapering down to match the lower rails. Gregrobo's, with the lower front overlap, and the intended cross over the rear weld joint is very, very well thought out. He has a lot of real experience, I think he's a boilermaker or some sort of practising tradesman.
Plate Y's give you facility for various thickness - like Gregrobo, 4mm in front, perhaps the same at the rear, or 3.85mm, then plate on the sides matching the OEM cradle wall thickness - usually, it's 3.175 / 180.
And, as I think I've pointed out in previous posts, perhaps in yours that had the pic of a frame in front of a roller door, Art / Craft cardboard IS Your Friend. Doing templates from those, gives you a lot of chances to try things out, and then minimises stuff ups with the actual plates you make. Plated Ys make it easy to make complicated shapes, to clear things like rads, hoses, if you need to.
You can either leave the pretty weld beads on, or with a good welder, that you let know what you want, you can have welding done to accommodate final linishing/filing to make the finished 'Y' look like a single piece. Outside corner welding lends itself to that final finish.
With the plated Y in the other thread you asked about, with the 'diamond' reinforcement plates, you can see that the side welds were not removed - you can see the bend / 'form over' the weld on the plate. The weld is visible on top of the Y / tube junction, it is nicely low profile, so it may indicate that there is also an insert, and it has been welded with a 'root gap' to get good penetration / fixation between the insert, plate and tube. Nice work.
I think in the post I mentioned above, I gave you suggestions with regards to the downtube. At the moment, I'm crook as a dog, having had a few metres of chemicals pumped into me a day ago, so I'm not up to back track to see what I wrote. I'll check it out soon. Not sure if what I've written here is intelligable, as I'm a bit out of it at the moment.
I'd take the overlap on the downtube higher ( no problem whatsoever with what he's done, I just tend to go for big engagement - or , idiot overkill as my mates call it), with a 'spear' shape, or a 'U' / 'V' shape at the top. Spear shape - full weld. Longer weld area, without a weld going across the front of the downtube. I've mentioned the risk of welds across a tube in other posts, but, sometimes they are unavoidable. And of no concern.
'U' or 'V' shape, can weld down inside the 'V', same with the 'U', although you could leave the 'inner U' unwelded. I think the downtube gets thinner as you go higher, so if you went high with overlap, you could just go for a very long engagement of the plate, with weld all the way, just up the side / edges. Just a bit of sealant at the unwelded section, would keep crud out, if you chose to go that way.
I'd put a rosette weld on, the base of which I'd have probably an inch away from the edge in the OEM downtube on there. If you had very long engagement, with no cross weld, perhaps another, small rosette weld towards the top, would be the go.
As you can see, with Gregrobo's and others, you can get a very large section Y made, with a lovely shape tapering down to match the lower rails. Gregrobo's, with the lower front overlap, and the intended cross over the rear weld joint is very, very well thought out. He has a lot of real experience, I think he's a boilermaker or some sort of practising tradesman.
Plate Y's give you facility for various thickness - like Gregrobo, 4mm in front, perhaps the same at the rear, or 3.85mm, then plate on the sides matching the OEM cradle wall thickness - usually, it's 3.175 / 180.
And, as I think I've pointed out in previous posts, perhaps in yours that had the pic of a frame in front of a roller door, Art / Craft cardboard IS Your Friend. Doing templates from those, gives you a lot of chances to try things out, and then minimises stuff ups with the actual plates you make. Plated Ys make it easy to make complicated shapes, to clear things like rads, hoses, if you need to.
You can either leave the pretty weld beads on, or with a good welder, that you let know what you want, you can have welding done to accommodate final linishing/filing to make the finished 'Y' look like a single piece. Outside corner welding lends itself to that final finish.
With the plated Y in the other thread you asked about, with the 'diamond' reinforcement plates, you can see that the side welds were not removed - you can see the bend / 'form over' the weld on the plate. The weld is visible on top of the Y / tube junction, it is nicely low profile, so it may indicate that there is also an insert, and it has been welded with a 'root gap' to get good penetration / fixation between the insert, plate and tube. Nice work.
I think in the post I mentioned above, I gave you suggestions with regards to the downtube. At the moment, I'm crook as a dog, having had a few metres of chemicals pumped into me a day ago, so I'm not up to back track to see what I wrote. I'll check it out soon. Not sure if what I've written here is intelligable, as I'm a bit out of it at the moment.